10 Considerations When Using Additive Manufacturing To Create Passive RF Components

By John Oncea, Editor
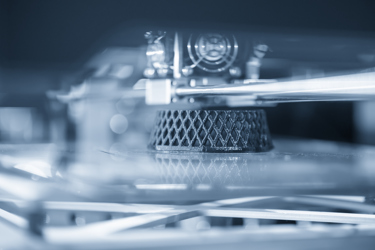
Engineers have started adopting additive manufacturing techniques to fabricate RF components. As a result, they are now able to customize components for better performance and system-wide efficiency, thanks to the increased flexibility that additive manufacturing provides.
Additive manufacturing (AM) refers to the use of 3D printing technology as a part of a complete workflow to produce fully functional parts. This digital process involves building parts layer by layer, without the need for hard tooling such as molds or cutting tools. It is a highly efficient and cost-effective way of producing complex designs and components.
Is it the same as 3D printing? According to Additive Manufacturing, “Some say yes, and we say no! AM and 3D printing are overlapping terms but not synonyms. 3D printing is the operation at the heart of additive manufacturing, just as ‘turning’ or ‘molding’ might be the operation at the heart of a conventional manufacturing process.
“In a nutshell, 3D printing is one step in an overall additive manufacturing workflow that also includes design, build preparation, postprocessing, business considerations, and more.”
Although some people associate AM with prototyping, this view is no longer accurate. Nowadays, 3D printing is a well-established method for creating tooling for many conventional processes. Moreover, manufacturers are increasingly adopting AM for production, including full-scale production.
However, the parts produced through additive manufacturing are not typical components that we are used to seeing. The best use cases for AM are new components that realize new ideas that cannot be made in any other way. 3D printing allows for geometric complexity, which makes it possible to consolidate, lighten, and improve on the designs of many conventionally made parts and assemblies.
However You Define It, It’s Being Used In RF
AM technologies such as inkjet printing, 3D printing, and screen printing can be used to create low-cost RF circuit patterning. AM also can be used to shape parts for more effective signal filtering. Several of the benefits of using AM for RF components include:
- Flexibility: Engineers have greater flexibility to tailor their RF components for performance and system-wide efficiency
- Performance: Additively manufactured RF components can perform as well or better than machined surfaces
- Cost: AM can reduce the cost of RF components and antennas
- Weight: AM can reduce the weight of RF components and antennas
- Fabrication time: AM can reduce the fabrication time of RF components and antennas
One application of AM is for RF passive hardware in telecommunications satellites, notes Nature, which cites the use of an FDM process by researchers at UC Berkeley “to 3D print passive components and a 0.53 GHz wireless sensor using a multiple-nozzle 3D printing system. Their process still needs to be perfected and the components need to be further miniaturized. Still, these components can be fabricated to have a broad range of resistance, capacitance, or inductance values. Other companies, like AT&S, are leading the way in commercializing these capabilities.”
What To Consider When Evaluating AM
A passive component, also known as a passive device, is an electronic component that can only receive energy, which it can either dissipate, absorb, or store in an electric field or a magnetic field. Passive components do not need any form of independent electrical power to operate. Applying AM to the production of passive RF components presents both opportunities and challenges.
Here are some considerations when using additive manufacturing for passive RF components:
- Material Selection: Choose materials with suitable electrical properties for RF applications. Conductive materials such as copper, aluminum, or specialized RF conductive filaments may be used. The dielectric properties of the material should also be considered.
- Printing Technology: Different additive manufacturing technologies have varying resolutions and capabilities. Select a printing method that can achieve the required precision for RF components. Stereolithography (SLA) and selective laser sintering (SLS) are commonly used for high-resolution parts.
- Design Considerations: RF components often have specific geometric shapes and sizes to meet frequency and performance requirements. Use design software that allows for precise control over the geometry of the component. Consider the layer-by-layer nature of 3D printing and its impact on RF performance.
- Surface Finish: The surface finish of 3D-printed parts can affect their electrical properties. Post-processing techniques, such as polishing or coating, may be necessary to achieve the desired surface smoothness for RF components.
- Testing and Validation: Thoroughly evaluate the 3D-printed RF components to ensure they meet the required performance specifications. This may involve using RF testing equipment to measure parameters like impedance, insertion loss, and return loss.
- Integration with Traditional Manufacturing: Consider how 3D-printed RF components will integrate into existing systems or assemblies. It's possible that a hybrid approach, combining additive manufacturing with traditional manufacturing methods, may be suitable for certain applications.
- Frequency Considerations: The frequency range of the RF components is crucial. Higher frequencies may pose additional challenges due to the wavelength and the need for tighter tolerances. Careful design and testing are essential to ensure the components perform as expected.
- Regulatory Compliance: Ensure that the 3D-printed RF components comply with relevant industry standards and regulations, especially if they are intended for use in commercial products.
- Prototyping and Iteration: Take advantage of the rapid prototyping capabilities of additive manufacturing. Iterate on designs quickly to optimize the performance of RF components before moving to mass production.
- Cost Considerations: Evaluate the cost-effectiveness of using additive manufacturing for RF components, considering factors such as material costs, equipment, and production time. In some cases, it may be more economical for mass production, while in others, it may be ideal for prototyping or low-volume production.
By carefully addressing these considerations, you can leverage additive manufacturing to produce customized and complex passive RF components that meet the specific requirements of your wireless communication system.