Exploring Current Test And Measurement Trends And Innovations

By John Oncea, Editor
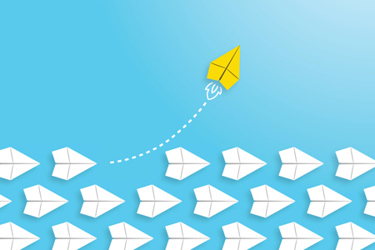
The test and measurement industry is evolving, driven by technologies like Industry 4.0, AI, and ML, all providing a competitive edge.
You’d be hard-pressed to find a market – semiconductors, automotive, aerospace, to name a few – that doesn’t rely on the test and measurement (T&M) industry. The need to ensure that manufactured products work as they should is both a legal and moral imperative, making sure the products are safe, compliant, and of high quality.
Want proof? Look no further than this MarketsandMarkets report which expects the T&M equipment market – currently worth an estimated $34.3 billion – to reach $42.9 billion by 2028, with a compound annual growth rate (CAGR) of 4.6%. Other sources project that the market will reach $44.92 billion by 2030, with a CAGR of 4.6% from 2024–2030. This growth is being driven in part by the growing adoption of electronic devices, surging deployment of advanced networking and communication technologies, and rising demand for high-performance and power-efficient electronic devices.
Developing technologies are also contributing to the burgeoning growth of the T&M industry, adds Research and Markets. These technologies include artificial intelligence (AI) and machine learning (ML), 6G, test-operation software, digitalization, autonomous vehicles, Internet of Things (IoT), and additive manufacturing.
“The growth of research and development activities across industries is also driving the demand for electronic test equipment writes,” Power Systems Design. “R&D labs, universities, and research institutions all need advanced measurement solutions for prototyping, characterization, and validation of new technologies and products.”
As the T&M market grows, sustainability and time-to-market will be critical for gaining new customers and retaining existing ones and Research and Markets suggests a holistic approach will be the path to acquiring a larger market share.
T&M Applications And Challenges
“T&M equipment requires precision machined components to perform accurate testing and measurements of torque, force, pressure, current, surface finish, and dimensions,” writes Pioneer Service. “By providing accurate information, these components ensure enhanced technology, better quality products, and cost savings.”
The types of testing and precision lab equipment used depend on the application and industry. Typical applications include load monitoring, CTE testing, strain gauge material testing, residual test analysis, and thermal stress analysis. Some industries currently using this equipment are oil & gas and hydraulics, as well as:
- Automotive: Infotainment systems, driverless vehicles, simulation for autonomous driving, wireless communications (LTE and Wi-Fi), hydraulic systems, and collision avoidance.
- Aerospace: DAQ systems, flight simulations, mapping, hydraulics, pressure monitoring, and surveillance.
- Semiconductors: Testing and monitoring equipment for, digital, analog, traditional, RF, and protocol-based requirements
- Medical: With an increasing demand for advanced medical devices and treatments, test and measurement equipment ensure health compliance and safety of diagnostic machinery, measurement of liquids and solids for pharmaceutical manufacturing, implants, and more.
In T&M, various machined parts are required, such as pins, bolts, screws, clips, hose fittings, pressure relief components, and gage components. Additionally, some customers may require shafts, bushings, nuts, poppets, seals, nozzle and valve components, and a wide range of custom fittings and fasteners.
“When building precision lab equipment and testing equipment, one of the key challenges is to create parts that provide highly accurate readings and measurements,” Pioneer Service writes. “However, as manufactured components become more complex, and applications become more demanding, older testing tools may not provide good measurements based on the component’s intended application. The manufacturing of precision testing equipment requires the use of the latest technologies and processes so that the final product can be easily verified to meet industry standards (ISO, FDA, etc.).”
Precision machined and turned components can help address many issues with their tight tolerances, high repeatability, and complex features. These parts can be made from a variety of materials and undergo various finishing techniques to provide longer wear in harsh environments. Some of these finishing services include electroplating, grinding, heat treating, and laser engraving.
T&M Trends
T&M drives the electronics market, Power Systems Design writes, adding that if you can’t make decisions or improve, correlate, and quantify something if you can’t measure it. “Common T&M equipment includes oscilloscopes, spectrum analyzers, power meters, and thermal imaging cameras, as well as environmental test equipment, network testers, electronic loads, and hipot testers. These instruments are used to measure required parameters such as voltage, current, resistance, signal integrity, loop stability, and more to make sure end products are safe and dependable.”
The current trends in T&M require instruments that are more portable, smaller in size, and lighter in weight. These instruments need to have greater networking and connectivity capabilities to easily integrate into ATE systems. Nowadays, most equipment provides multiple features and functionalities that used to require multiple types of test equipment, all available in one instrument. Other trends include offering greater precision, accuracy, resolution, and reliability than ever before.
“Most recently, there has been a shift toward software-defined and cloud-based test and measurement solutions that enable more flexibility, scalability, and remote access,” writes Power Systems Design. “Additionally, there is a growing focus on data analytics and automation to streamline testing processes and extract valuable insights from the raw test data.”
Another trend driving T&M growth is the principles of Industry 4.0 and the aforementioned IoT, both of which are helping to integrate T&M with smart and connected systems, reports Verified Market Reports. Test instruments equipped with IoT capabilities enable remote monitoring, data logging, and real-time analytics. This enhances productivity and efficiency in manufacturing and R&D environments. Industry 4.0 concepts such as predictive maintenance and digital twins leverage data from test equipment to optimize production processes, reduce downtime, and improve product quality.
“The demand for high-speed and high-bandwidth testing solutions is increasing across various industries, driven by the proliferation of high-speed data interfaces, wireless communication standards, and emerging technologies such as 5G, automotive radar, and IoT devices,” Verified Market Reports continues. “T&M equipment with enhanced bandwidth capabilities, such as oscilloscopes, signal analyzers, and network analyzers, enable engineers to characterize signal integrity, validate high-speed interfaces, and troubleshoot complex communication systems with unprecedented accuracy and speed.”
AI and ML are also transforming the way T&M processes are conducted by making it possible to use predictive analytics, automated test routines, and intelligent decision-making capabilities. With the help of AI-powered algorithms, vast amounts of test data can be analyzed, patterns identified, and test parameters optimized to improve measurement accuracy, reduce test times, and enhance productivity. ML techniques enable adaptive testing strategies, anomaly detection, and predictive maintenance, which empowers engineers to make data-driven decisions and optimize product performance throughout its life cycle.
Verified Market Reports adds the rise of modular and software-defined instruments, emphasis on high-speed and high-bandwidth testing, focus on environmental and EMC testing, and the transition toward portable and field-deployable instruments and trends to be aware of.