How Space Agencies Keep Electronics Safe In The Final Frontier

By John Oncea, Editor
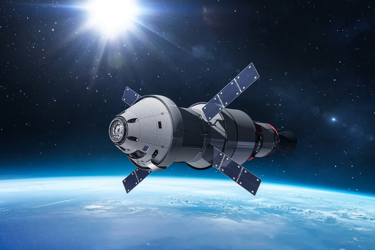
Safety is job one, something that is especially true in the harsh environment of space. With so many ways for electronics to go bad, what is being done to keep us safe when exploring the heavens?
Space is the final frontier, the place where no one can hear you scream, and only an hour's drive away if your car could go straight upwards. It’s also an incredibly harsh place, not only for the more than 650 people who have been there – including three Soyuz 11 cosmonauts who died during reentry – but for the machines and components we rely on to get there.
Take electronics, for example. The reliability of electronic components is highly dependent on the environment in which they operate and, as we know, space may just be the harshest of environments.
The changes in temperature and other ambient conditions in space can cause alterations in material behavior and even lead to component failure. Other conditions that pose challenges for electronic circuits in space, according to Cadence Design Systems, include:
- Pressure: There is zero pressure in space and components manufactured under atmospheric pressure may behave differently under such no-pressure conditions.
- Ion and particle presence: In the space application for low earth orbits, UV radiation causes molecular degradation of helium, oxygen, nitrogen, etc. The atomic versions of these elements initiate corrosion and erosion of materials. The ions and free electrons in space can cause arching, which may affect sensitive electronic components.
- UV degradation: UV degradation changes the composition of materials and can even remove oxygen from materials, thereby affecting the performance of the components.
- Radiation: The free-particle radiation environment can introduce single-event glitches that may challenge the operation of sensors and controls in electronic circuits.
- Extreme temperature and thermal cycles: Extreme hot and cold temperatures and thermal cycles impose mechanical stress on electronic components, especially ICs and their packages.
Add in the fluctuating pressures associated with acoustic energy during launch which can cause vibration of structural components over a broad frequency band ranging from 20 Hz to 10,000 Hz and above and it’s overwhelmingly impressive how successful we’ve been sending people into space.
Much of that success is due to the work of space agencies around the world, including NASA. But what, exactly, are these agencies doing to protect the electronic systems needed to thrive in space safe from the harsh environment the machines they help power operate in?
Knowing What The Dangers Are
There are many threats to electronic circuits in space including circuit board damage that can result in electrical shorts caused by shocks and vibrations during launch and separation. “The jerking of the circuits may cause loose connections or connector failures,” Cadence Design Systems writes. “The loss of data transfer or control due to loose connections or intermittent connections can be disastrous in space applications. Another mechanical vibration-induced failure challenging space electronic applications is the resonance in electronic components, which should be addressed to ensure reliable missions.”
Outgassing, reduced life and operational functionality, and tin whiskers are three other dangers singled out by Cadence Design Systems. Outgassing refers to the release of gases by non-metallic materials, such as thermal paste, plastics, glues, or PCB materials.
These gases can deposit on other components and negatively impact their performance. In some cases, the vapors released from these materials can even cause short circuits between leads, connectors, and components. Shorts also can be caused by tin whiskers grown in the vacuum of space out of the tin, cadmium, and zinc that make up electronic components.
Temperatures are extreme in space and this adversely affects electronic circuits, shortening a component’s lifetime and significantly limiting its operational functionality. When commercial off-the-shelf components are subjected to temperatures above or below the allowable range, it can lead to failure.
How We’re Protecting Electronic Circuits And, More Importantly, Humans
Traditionally, space agencies use several techniques to protect electronic circuits in space. To keep electronics cool, radiators are used to radiate heat away from the equipment. Another method is the use of thermoelectric cooling, which uses the Peltier effect to transfer heat from one side of a device to the other. These methods are used on spacecraft and satellites to dissipate the heat generated by the electronic equipment.
The Planetary Society notes other methods include:
- Potting, which involves filling the electronic assembly with a solid or gelatinous compound to resist shock and vibration.
- Silicon on insulator in which chips for space usage are manufactured on an insulating substrate instead of a silicon one, allowing them to be more radiation-resistant and fault-tolerant.
- RAM types, noting that Static RAMs (SRAM) are preferred instead of Dynamic ones (DRAM) because they are less power-hungry. This is crucial for when spacecraft go into low-power modes but need to continue sending telemetry data.
- External shielding like lead around the electronic components that reduces radiation exposure thereby increasing the life span of the mission. This is particularly useful in long-term missions.
Another costly, less-desired option is multiple copies, or placing several copies of a critical component on a satellite so that if one fails, the others can pick up the slack.
More recently, NASA and The European Space Agency (ESA) have turned to 3D printing, developing new and improved electronic components, and leveraging quantum materials for next-generation space electronics.
“Printed electronics involves 3D printing a variety of electrically active materials such as metals or carbon-doped polymers to form devices like transistors, capacitors, and resistors, plus the electrical connectors linking them together,” writes ESA.
“Printed and flexible EEE components are fast rewriting the future of electronics,” explains ESA Internal Research Fellow Rita Palumbo, overseeing a new working group on the topic. “So, we are looking into how space could benefit from this step change.”
EEE parts can be printed in any shape using flexible substrates, making complex geometries possible, which is difficult with traditional manufacturing. They are also cheaper and are printed onto thin substrates and can be printed on existing hardware or structural surfaces. Utilizing 3D printing opens up a new design dimension, allowing the creation of novel stacked or embedded integrated circuits. The major appeal is that 3D printing opens the prospect of the repair and production of parts in locations such as the International Space Station, the Moon, or Mars.
NASA, according to Interesting Engineering, is also working on printing electronic parts in space, something they say will “revolutionize spacecraft design, save space, and enhance communication capabilities, opening up new frontiers for exploration and discovery.
“The concept is simple yet powerful – instead of conventional electronics modules, they developed hybrid printed circuits that could be fabricated directly onto the spacecraft's structure. These circuits were so thin that the human eye couldn't even discern their existence, with traces measuring just about 30 microns, half the width of a human hair. The potential benefits of this technology are immense, ranging from saving valuable space on board to enhancing antenna and radio frequency applications.”
The use of quantum materials for future electronics, according to the University of Geneva, holds a promising future thanks to “their unique properties – especially the collective reactions of the electrons that compose them. These quantum materials could be used to capture, manipulate, and transmit information, carrying signals (for example photons, in the case of quantum telecommunications) within new electronic devices. Moreover, they can operate in electromagnetic frequency ranges that have not yet been explored and would thus open the way to very high-speed communication systems.”
‘‘One of the most fascinating properties of quantum matter is that electrons can evolve in a curved space. The force fields, due to this distortion of the space inhabited by the electrons, generate dynamics totally absent in conventional materials. This is an outstanding application of the principle of quantum superposition,” explains Andrea Caviglia, full professor at the Department of Quantum Matter Physics in the Faculty of Science of the UNIGE and last author of the study.